Thermal Spray Coatings
When it comes to Thermal Spray Coatings, look no further than the experts at Techmetals, Inc. Boasting over 50 years experience in providing certified metal plating and coating solutions, we are your one-stop resource for a variety of thermal spray technologies and services, including:
- High-Velocity Oxy Fuel (HVOF)
- Air Plasma Treatments
- Twin-wire Arc Spray Coatings
- Precision Machining/Grinding
Thermal spray coatings are often used to help prevent devastating issues such as wear, erosion, abrasion and corrosion of
integral parts that demand flawless function and reliability.
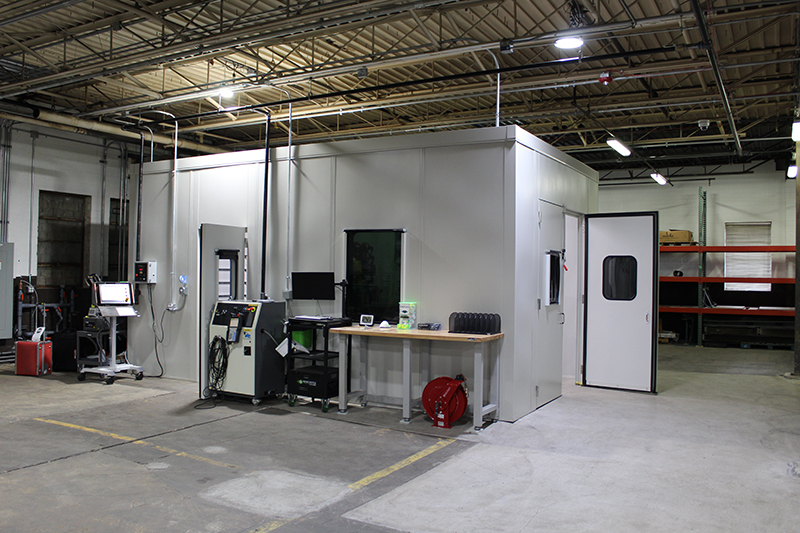
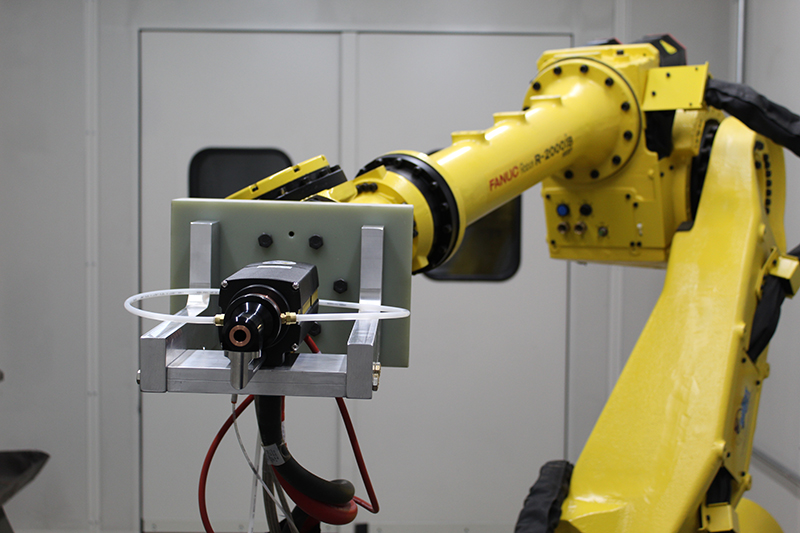
This specialized spray offers unique versatility and benefits in repair & restoration capacities, as well as with new parts — most commonly in seen in the aviation, oil & gas and power generation markets. But it also is utilized in fields such as pulp and paper, automotive, marine and other industrial capacities.
Thermal sprays have become highly specialized due to many technological advancements in recent years, and Techmetals is proud to accommodate our clients with a number of coating types including metals, ceramics, ceramets and different combinations of each to meet their needs.
Techmetals engineers specialize in creating thermal coating combinations to meet your exacting requirements — eliminating unwanted heat transfer to your products. Discover peak performance from each of your parts with our thermal spray solutions today!
HIGH-VELOCITY OXY FUEL (HVOF)
Providing the highest bond strength and coating density, HVOF thermal spray is one of the most popular processes to help enhance or restore a component’s surface. High-velocity Oxy Fuel offers tailored solutions to better extend the life of your parts, improving the wear and erosion resistance of each.
This coating also adds corrosion protection typically by incorporating Tungsten carbide blends. Literally hundreds of thermal spray materials are available, allowing for a wide variety of options to create the perfect high-velocity surface for your equipment.
HVOF solutions help address the following:
- Wear and Erosion
- Abrasion
- Adhesive Wear
- Cavitation
- Hard Chrome Replacement
- High Temperature Environments
- Corrosion Resistance
- Atmospheric Environments
- New Part Manufacturing
- Cathodic Protection
- Chemical Environments
- Friction Engineering for Fretting
- Galling
- Anti-skid/Traction
- Tribological Coatings
- Dimensional Restoration of Parts Requiring Repair
AIR-PLASMA THERMAL COATINGS
Plasma Thermal spray solutions have a high-flame temperature, making this option extremely versatile. Perfect compatibility with all sprayable ceramics, as well as with virtually all metal and ceramic materials, our air plasma treatments offer amazing wear properties.
Typical applications consist of Tungsten or Chrome Carbides, but other materials are also available, such as Aluminum Oxide, Ziconium Oxide, Titanium Dioxide, Chromium Oxide and Magnesium Zirconate.
Air Plasma coatings help address the following:
- Wear and Erosion
- Abrasion
- Adhesive Wear
- Cavitation
- Hard Chrome Replacement
- High Temperature Environments
- Corrosion Resistance
- Atmospheric Environments
- New Part Manufacturing
- Cathodic Protection
- Chemical Environments
- High Temperature Environments
- Thermal Barrier Coating Requirements
- Electrical/Conductive Insulating Properties
- Bio-compatible Requirements
- Dimensional Restoration of parts requiring repair
TWIN-WIRE ARC SPRAY (TWAS)
This economical spray process offers an excellent barrier layer for not only protecting components from deterioration, but also enhancing it’s lifespan. Depositing a high-performance thermal coating, Twin-wire Arc Spray is a perfect solution for part restoration.
Common materials for TWAS can include:
Nickel/Aluminum — Nickel/Aluminum/Moly — Stainless Steel — Moly — Ni/Chrome/Aluminum/Yttrium — and Aluminum.
TWAS solutions help address the following:
- Wear and Erosion
- Abrasion
- Adhesive Wear
- Cavitation
- Hard Chrome Replacement
- High Temperature Environments
- Corrosion Resistance
- Atmospheric Environments
- New Part Manufacturing
- Cathodic Protection
- Chemical Environments
- Friction Engineering for Fretting
- Galling
- Anti-skid/Traction
- Tribological Coatings
- Dimensional Restoration of Parts Requiring Repair