Hard Chrome Plating
As a matter of fact, Hard chrome plating is one of the most reliable and widely used finishing processes in the industry. To that end, this plating is typically used to help resist abrasion and corrosion. Additionally, industrial hard chrome also helps improve a part’s wear.
Chrome plating generally offers deposit thicknesses of > 0.1 mil, and up to 20 mils or more.
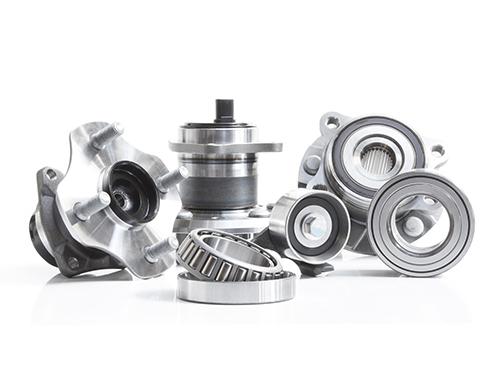
By and large, the application of hard chrome provides moderate corrosion and oxidation protection for the coated substrate. Also, it is especially effective when applied to the cavities of molds, dies, tools and other components where the processing of abrasive resins exist.
Consider Techmetals for your industrial hard chrome repair or salvaging of older parts, molding dies, aircraft engine parts and more.
Hard Chrome Plating Benefits:
- Wear Resistance
- Part Repair
- Corrosion Protection
- Non magnetic
- Easily applied over any finish,
mimicking the base substrate
Specifications:
QQ-C-320, AMS-QQ-C-320, AMS 2460, AMS 2406, MIL-STD-1501, ASTM B 177
MPR 1059 Nickel Chrome: (NAVAIR/NAVSEA/NAWCAD)
NUCLEAR SPECS:
MIL-DTL-23422
Hard Chrome Properties:
PROCESSING TEMP:
128-140° F
HARDNESS:
68-72 Rockwell
MELTING POINT:
1900° C
DENSITY:
6.9 g/cm3
Techmetals Engineered Hard Chrome Finishes
Since it becomes a part of the metal itself and will not chip, peel, crack or flake — Armatech is a popular coating. When run through standard bend tests, it continues to resist these issues as well.
Additionally, Armatech will not affect dimensions by more than .0002″ per surface. It is recommended as a final process eliminating additional grinding and finishing operations for example.
With this in mind, it is designed for sliding wear in metal-to-metal applications — with excellent ability to retain lubricants.
When comparing to standard hard chrome plating, TM105 is brighter, harder and more corrosion resistant .
Also, deposits can be plated up to 71 Rockwell C compared to standard chrome, which ranges from 64 to 67 Rockwell C. It’s brightness and low coefficient of friction make it ideal for molds and metal cutting tools for example.
In summary, TM105 is best known for its release, excellent wear, and anti seizure characteristics.
Firstly, TM111 is an Electroless Nickel (EN) with a Hard Chrome deposit overlay. Secondly, the base of the EN provides a uniform corrosion resistant, barrier coating.
Therefore, the TM111 EN Hard Chrome plating provides a hard, wear resistant surface. This deposit is usable on all ferrous and most non-ferrous metals.
To clarify, TM119 is a specially engineered, dense hard chrome with the intention of impregnating it with PTFE (polytetrafluroethylene).
By doing so, PTFE enhances the release, wear and corrosion properties of the chrome.
Furthermore, it is most common in chrome deposits needing additional release and a low coefficient of friction — such as metal forming, tooling and molds for example.
In short, TM121 is a crack-free, chromium deposit offering good corrosion resistance. Comparatively, standard hard chrome has approximately 200 to 400 cracks per linear inch — allowing corrosive material through to attack the base metal.
To clarify, TM121 crack-free, hard chrome is a barrier coating — depositing somewhat in a softer and more ductile manner than standard industrial chrome.
As deposited, it is matte gray but may be polished to a bright finish. It is often used in direct contact with molten glass.
Diamoforce is one of Techmetals’ latest, hard chrome alloy plating technologies. Firstly, this coating has extreme hardness and an amazing wear resistance.
Secondly, Diamoforce provides a slick surface that reduces the coefficient of friction. Additionally, this alloy reduces galling and improves lubricity.
The deposit has a unique nodular structure, which provides for it’s excellent wear characteristics. Lastly, Diamoforce is a great non-stick solution that helps resist corrosion.
As a matter of fact, Splatter Guard is one of Techmetals’ latest advances in coating technology. Coupled with it’s exceptional wear corrosion resistance and release, TM107 offers a very hard coating.
In short, Splatter Guard conforms to the base metal. Thickness is typically .0001”-.001”, although it may be varied slightly outside of these parameters to meet your needs.
Also, Splatter Guard as deposited, has a coating hardness of 66-70 Rockwell C. To this end, it exhibits a low coefficient of friction and anti-galling properties. In most applications, it will last 2 to 10 times longer than other parts or processes. It will not fill in or cover up blemishes or scratches however.
In particular, the TM-Rx process is precisely controlled by our lab staff and engineering team. Furthermore, TM-Rx is a medical-grade, chromium coating helping to prevent wear, galling and corrosion. Parts and instruments with this coating are designed to work and look like new after 1,000 cycles in an autoclave.
What’s more, TM-Rx meets or exceeds ISO 10993-1 Certification, as well as the principles governing the biological evaluation of medical devices. Certified report numbers: 331553, 331617, 331621 and 331555.